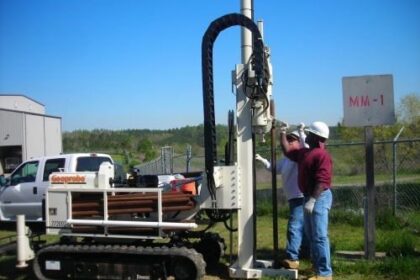
A Phase II Environmental Site Assessment (ESA) is the second step of investigation into whether a property has environmental contamination of some kind. A Phase II ESA reflects the suspicion of an environmental consultant that contamination exists based on a Phase I ESA. While completing the Phase II ESA, the consultant will confirm or exclude the presence of contamination with laboratory data taken during the investigation. The report will provide the documented results.
Table Of Contents
Executive Summary Phase I ESA – Findings (REC)
The first thing you need to know is you only need a Phase II ESA if the findings of your Phase I1 ESA come back with what are known as a REC, Recognized Environmental Condition. You can find the Phase I ESA findings in the front of the report in the executive summary. It’s fairly easy to read and only a few pages long. If you find it confusing, call your environmental consultant who should be happy to take the time to explain the results to you. Odds are low that any property will need a Phase II ESA but those odds rise with the type of building we are talking about. Anything with dry cleaning, automotive or metals production is suspect. If the building is industrially zoned or has served in an industrial capacity, that’s another thing that would raise the odds of a Phase II ESA.
Phase II ESA Scope
“Scope” refers to exactly what the Phase II ESA will do. What the environmental consultant is looking for, where they are looking for it, how many samples they are taking, what kind of equipment they will use are all elements that drive cost. We’ll talk a lot more about this below but I cannot overstress the point that you need to have a long honest talk about what you are trying to accomplish before settling on a scope for the project. Scope determines the price of the project. Narrow scopes make lower prices and wider scopes make higher prices but if you think less expensive is better you might want to rethink that. A scope for a Phase II ESA can be narrowed so far that if the land owner wants to go for regulatory closure, the information gained in the narrow Phase II ESA is not extensive enough to turn into the state. This means that cheaping out on a Phase II ESA might wind up costing you a second trip with a wider scope Phase II ESA to satisfy the government regulators. I can tell you from experience, two Phase II ESA will always be more expensive than one. It’s better to get it done right the first time, even if the first time is marginally more expensive.
Phase II ESA Equipment
Different types of Phase II ESA require different equipment.
- Photoionization Detector (PID) – This is an electronic ‘nose’ which sniffs the soil looking for volatile organic compounds. It’s a $4000 piece of scientific equipment.
- Ground Penetrating Radar (GPR) – This is a radar that shoots down into the ground and is handy for showing disturbed soil and the tops of leaking underground storage tanks. These hidden tanks are often the reason for a Phase II ESA.
- Electromagnetic Survey (EM) – This is similar to the GPR but it helps us find metal in the ground. Underground piping can lead to tanks and both are notorious leakers.
- Drill Rig – These drill rigs are often truck mounted, or skid-steer mounted heavy equipment for drilling shallow wells to test soil and groundwater.
- Backhoe Excavator – If we need to remove a tank, the best way to do it is with a backhoe. Both the drill rig and backhoe are heavy equipment with specialized skills needed to run them and trucks which deliver them to the jobsite.
Phase II ESA Laboratory
The Phase II ESA laboratory work is an expensive piece which drives the project cost. Laboratory analytical can be defined narrowly or broadly and the prices vary by the tests we run. We determine the tests to run against the soil and groundwater samples by what we are looking for. Are we likely to find oil, gas or diesel? Was it formerly a dry cleaner? Did the use acids and heavy metals? Depending on what we are looking for drives what we are sampling for.
Phase II ESA Geography
A Phase II ESA can happen over a small area or over an enormous area depending on if the plume of contamination traveled underground because of rainwater. How wide the area is determines how many holes we drill. How many holes we drill determines how many samples need testing in the laboratory and the whole project size determines how many hours we’ll be onsite. The bigger projects can turn into days and weeks of work. All of these factors drive the price.
Phase II Environmental Site Assessment Report
After we complete the work and get the analytical back from the lab, a report needs to be written to summarize our findings. In environmental consulting, reports are how all information is conveyed. They include the scientific backup data that drive our recommendations.
Phase III – Remediation
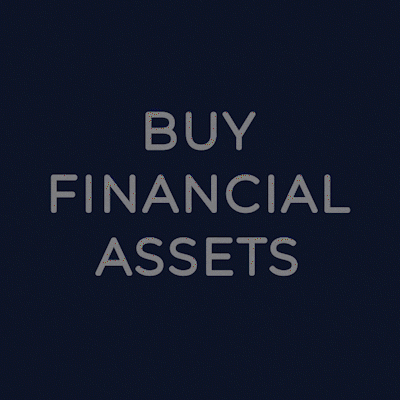
Assets Not Liabilities
It is possible that a Phase II Environmental Site Assessment Report puts to bed any concerns regarding contamination on a commercial property. In fact, I would say a full 50% come up with no detectable traces of environmental contaminants. Aside from the money you spent to get this answer, this is good news. Because if we find contaminants above the regulatory limits, the project needs to move to the remediation stage.
Dig & Haul – Often the best way to remediate a property is to dig out the soil and haul it to a landfill which is designed to hold contaminated soil. Chemical & Biological Remediation – These types of remediation mix in chemicals or bacteria to bond with the contaminants and neutralize them. Vapor Mitigation – This is a positive pressure system that keeps the volatile fumes from coming into the building through cracks in the foundation and the sump pump.
Types of Institutional Controls
Engineered Barrier – Engineered barriers are frequently used to contain contamination in place. A good example of a typical engineered barrier is a parking lot over the top of contaminated soil. The hardscape controls exposure to the contamination (i.e. ingestion, inhalation)
Other engineered barriers include capping contamination with a layer of clean soil, injecting a grout wall to prevent movement, or putting a building on top it.
Highway Authority Agreement – This is an agreement between the Remedial Applicant, IEPA, and any roadway authority (state, county or city), where contamination has migrated or has the potential to migrate under a roadway, and agree to leave it in place. The highway authority is made aware of the potential exposure to the contamination and can therefore protect its workers during future work.
Land Use Control – Depending on the levels of contamination with regard to TACO, a limitation to future uses can be added to the title of a property ensuring it won’t be used for residential, day care or hospital uses in the future.
Groundwater Use Restriction – Limiting future uses of potable water on the property is a method for eliminating the risk of exposure through groundwater ingestion. Several municipalities already have in place ‘Groundwater Ordinances’ prohibiting the installation or use of wells as a potable water source. For the City of Chicago, the IEPA it’s called a Memorandum of Understanding (MOU), which, if you’re in the marketing department is always followed by “SE!!” and then the whole Mickey Mouse Club theme song.
If you need a Phase II Environmental Site Assessment Report, research or testing done on your property or one you are interested in purchasing, give A3 Environmental Consultants a call. We’ll get your project done with the utmost in confidentiality, we’ll meet or exceed ASTM Standard E1903-19 on any sort of commercial or industrial property. Our Assessments meet the requirements of all lenders and government agencies such as the Small Business Administration (SBA), Housing and Urban Development (HUD) and the United States Department of Agriculture (USDA). A3 Environmental Consultants can be reached at (888) 405-1742 or by email at Info@A3E.com.